焊接作为汽车整车生产工艺中的重要环节,自动化程度是衡量整车厂生产水平的标志,今年九月焊接机器人的安装到位,神龙成都工厂焊接自动化率达到百分之百,这一技术水平将在国内遥遥领先。冲压车间内,最大承重达80吨的天车,在15.4米的高空吊装设备。先进的冲压设备,两条生产线,4台冲压设备,总价值约4亿元!这些设备的先进之处就在于,将汽车覆盖件的生产节拍,从每分钟8—10片提高到15—20片。冲压设备采用济南二机床。
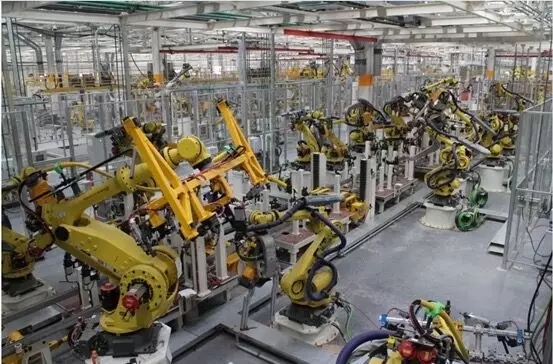
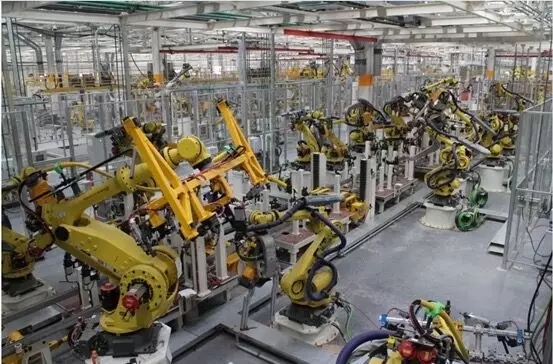
10月10号,神龙汽车成都工厂传出消息,焊装车间车身线于当日打通,标志着焊装车身线具有线外批量生产的能力。据介绍,焊装采用的激光焊技术是近年来新兴的焊接技术,成都工厂在开启件、前后端、车身线都采用激光钎焊、激光熔焊技术。焊装生产线主线全部柔性化设计,可以随机生产6种车型,柔性切换,设计节拍60台/时。435台机器人打造的100%自动化率高效率工厂直接生产工人不到100人,仅为同等规模传统汽车制造厂的1/10,工人劳动强度显著下降,劳动生产率大幅提高。自动化程度是焊接车间的最大特点。一辆白车身的厂内焊点达到2400多个,而整个通过320个机器人、81个夹具、44个转台,就能完成相关车型的生产任务。主车间实际操作人员仅75人,不足机器人数量的四分之一。
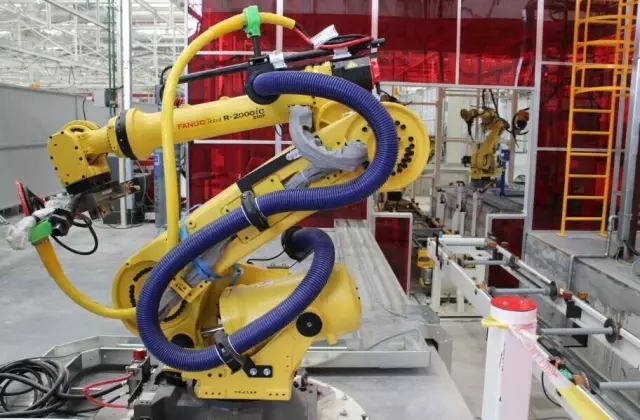
达产后每分钟可下线一台车
成都工厂焊装生产线广泛采用了目前汽车制造先进工艺和技术:激光熔焊/钎焊、自动弧焊、机器人螺柱焊、中频焊、无钉冲铆、自动防飞溅喷淋、高速输送辊床等,先进工艺技术的采用显著提高了产品质量,减少了返修,提高了生产率。成都工厂焊装工艺技术处于国内领先水平。
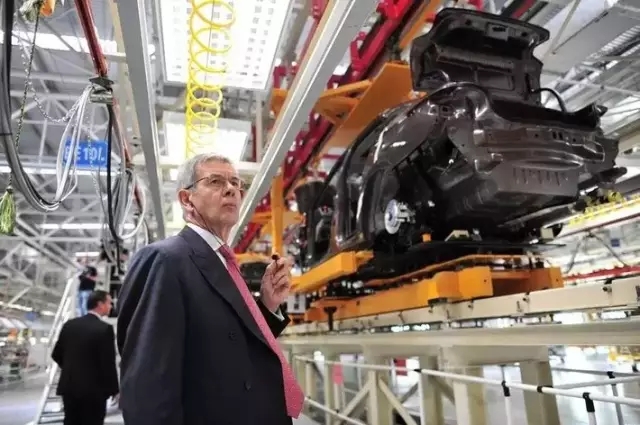
“一般来说在国内生产的合资厂商,焊装自动化率在50%左右,我们的焊装车间自动化率达到100%。处于世界领先状况。”焊接车间负责人孙继胜表示。据透露,车间采用机器人生产后,人工工位基本消失。车间的围栏由传统的铁丝网围栏换成了先进高分子PC透明塑料板,PC板视觉效果好,其不仅可以全方位隔绝人员进入,还兼有防火的功能。东风神龙成都项目于去年10月奠基,预计2016年建成投产,将贡献36万辆的产能,主要生产东风雪铁龙、东风标致和东风三个品牌车型,以高端SUV、MPV为主,车型与欧洲同步开发、同步投放。
据了解, 神龙汽车公司 成都乘车用项目位于成都市龙泉驿区,规划总投资123亿元,规划总产能32万辆,其中一期工程总投资79.05亿元。